Thursday, November 21, 2024
How to Build a Pallet Shed DIY for Your Backyard Garden
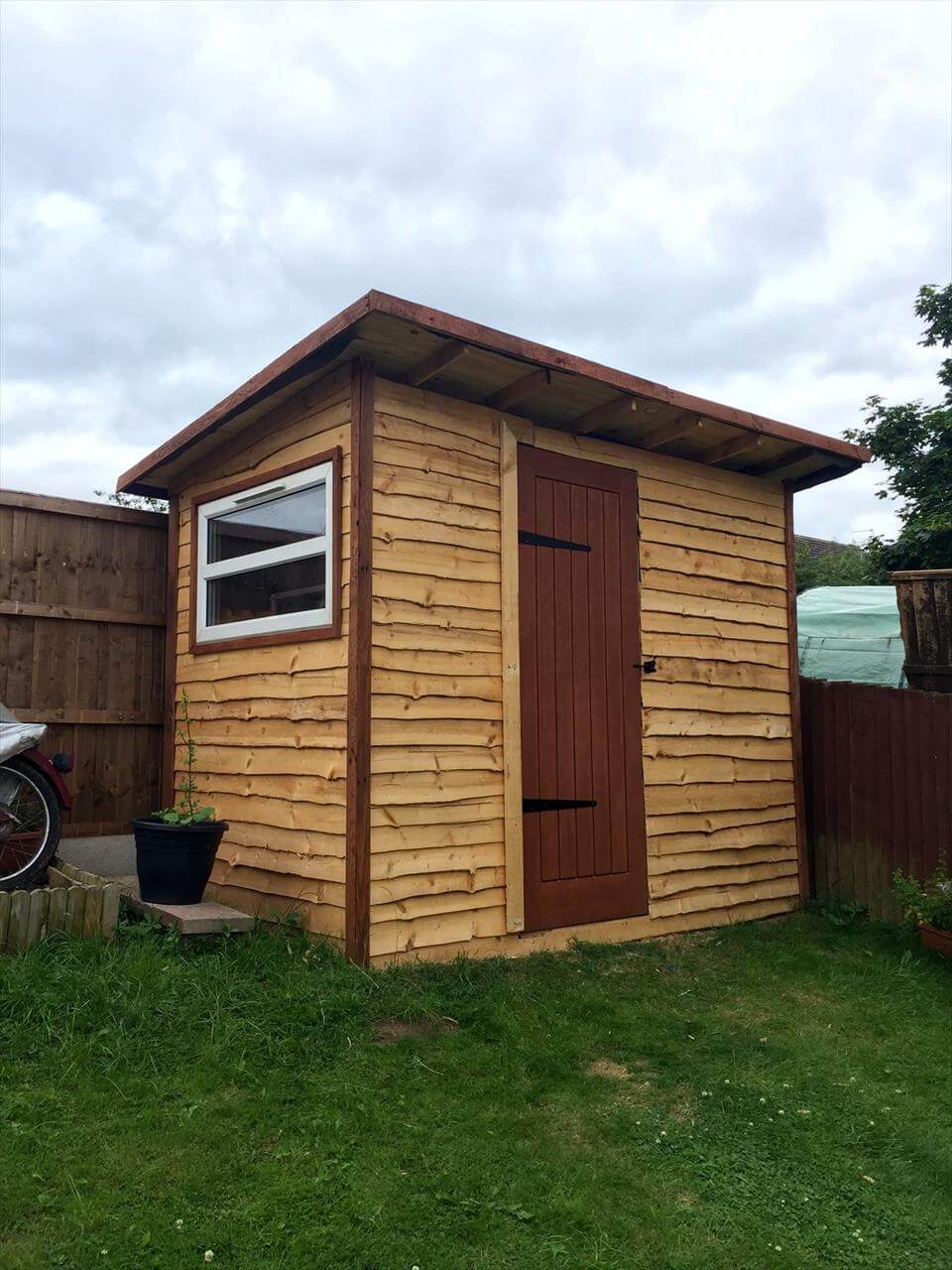
Building Your Dream Pallet Shed: A Backyard Oasis Awaits! Hey there, fellow DIY enthusiasts! So, you're dreaming of a cute little shed for your garden, somewhere to stash your tools, potting soil, and maybe even a comfy chair for a quiet afternoon? Forget those expensive pre-fab sheds â€" let's build something amazing, unique, and budget-friendly using reclaimed pallets! This isn't rocket science, I promise. With a little elbow grease and some [...]
DIY Wood Pallet Shed: How to Build a Shed with Minimal Cost
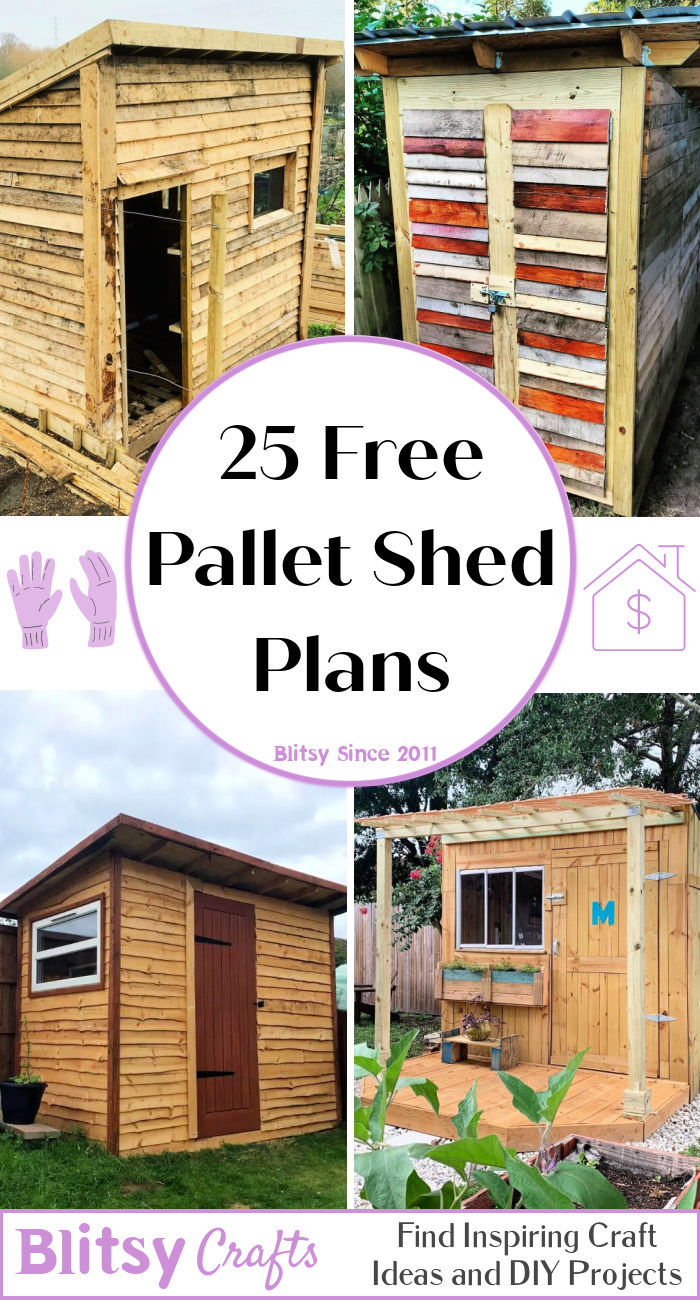
DIY Wood Pallet Shed: How to Build a Shed with Minimal Cost Hey there, fellow DIY enthusiasts! So you're dreaming of a shed, but the price tags at the home improvement stores are making your wallet weep? Don't worry, you're not alone! Building a shed from reclaimed wood pallets can be a fantastically affordable and surprisingly rewarding project. It's a great way to get that extra storage space you need without breaking the bank (or your back!). [...]
Step-by-Step Lean-To Shed DIY: Build a Sturdy Shed for Your Tools

Step-by-Step Lean-To Shed DIY: Build a Sturdy Shed for Your Tools Tired of tripping over garden tools and overflowing storage bins? A lean-to shed offers a simple, affordable, and surprisingly sturdy solution to your storage woes. This step-by-step guide empowers you to build your own, transforming a cluttered space into an organized haven. We’ll walk you through each stage, from planning and material selection to the final touches, ensuring [...]
Small Pallet Shed Plans: A Budget-Friendly DIY Project for Your Yard
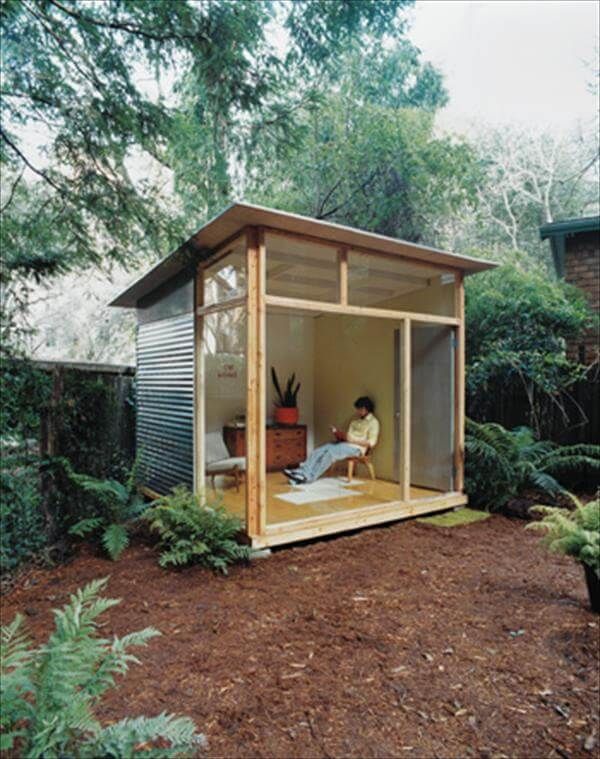
Small Pallet Shed Plans: A Budget-Friendly DIY Project for Your Yard Hey there, fellow DIY enthusiasts! Are you looking for a way to add some extra storage space to your yard without breaking the bank? Then you’ve come to the right place! Building a small shed from reclaimed pallets is a fantastic project that's both budget-friendly and surprisingly satisfying. I'm going to walk you through the process, sharing my tips and tricks along the [...]
Create a Simple Small Pallet Shed for Your Garden Tools and Equipment

Constructing a Simple Pallet Shed for Garden Storage This document details the construction of a small, functional shed utilizing repurposed pallets, providing a cost-effective and environmentally conscious solution for garden tool and equipment storage. The design prioritizes simplicity and ease of construction, making it suitable for individuals with basic carpentry skills. While this guide provides a comprehensive overview, readers should [...]
DIY Lean-To Shed: Step-by-Step Instructions for Your Backyard Shed
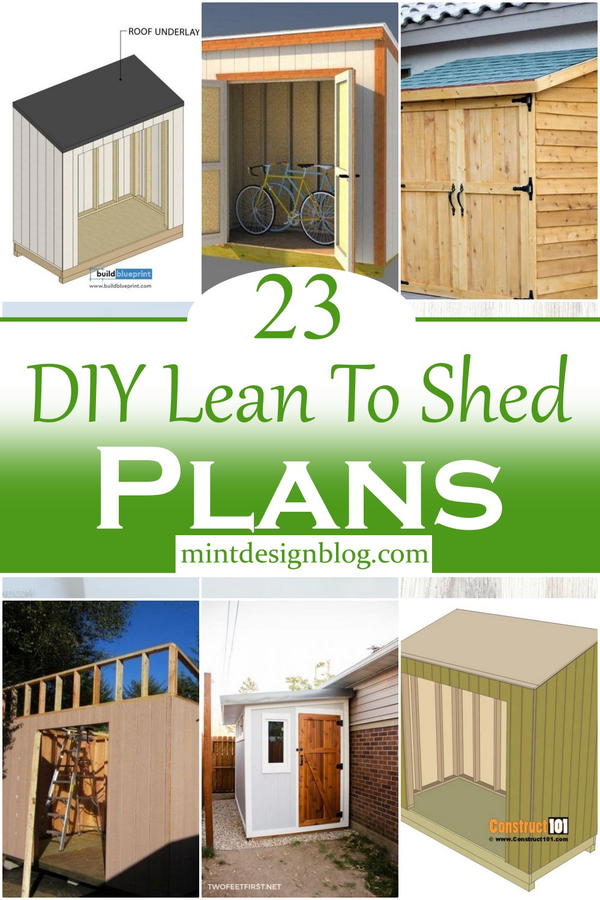
DIY Lean-To Shed: Your Step-by-Step Guide to Backyard Storage Building your own lean-to shed is a rewarding project that adds valuable storage space to your backyard while providing a fantastic opportunity to learn valuable DIY skills. This comprehensive guide walks you through each step, ensuring a successful build even for novice builders. Forget expensive pre-fabricated sheds; let's build something unique and tailored to your needs! Planning [...]
Saturday, November 16, 2024
Gardening Shed with Loft: 12x20 Plans

12x20 Gardening Shed with Loft: Comprehensive Design and Construction Plans This document provides detailed plans for the construction of a 12ft x 20ft gardening shed incorporating a loft for additional storage. The design emphasizes functionality, durability, and aesthetic appeal, suitable for a range of garden settings. The plans are intended as a guide and should be adapted to suit individual needs and local building regulations. Professional [...]
Monday, November 11, 2024
DIY Guide to Building a Pole Barn for Cold Weather Areas
Pole barns, with their robust construction and adaptable design, are increasingly popular choices for a wide range of applications, from garages and workshops to agricultural structures and even residences. However, in cold weather climates, building a pole barn requires extra considerations to ensure optimal performance and longevity. This guide delves into the essential aspects of building a pole barn specifically tailored for frigid temperatures, [...]
DIY Guide to Building a Pole Barn with Sliding Doors
Alright, folks, let's talk pole barns. These beauties are versatile â€" perfect for everything from workshops and garages to storage sheds and even cozy living spaces. And the best part? You can build one yourself, saving a ton of money in the process. Today, we're going to tackle the challenge of building a pole barn with sliding doors, making your space both practical and stylish. First Things First: The Planning Stage Before you dive [...]
DIY Guide: How to Build a Pole Barn with a Spacious Layout

A pole barn, with its robust construction and customizable design, offers a versatile solution for a multitude of purposes. Whether you envision a workshop, a storage facility, a garage, or even a charming living space, a well-planned pole barn can serve as a functional and aesthetically pleasing addition to your property. This guide will equip you with the knowledge and step-by-step instructions to confidently embark on the journey of building [...]
How to Design and Build a Custom Pole Barn
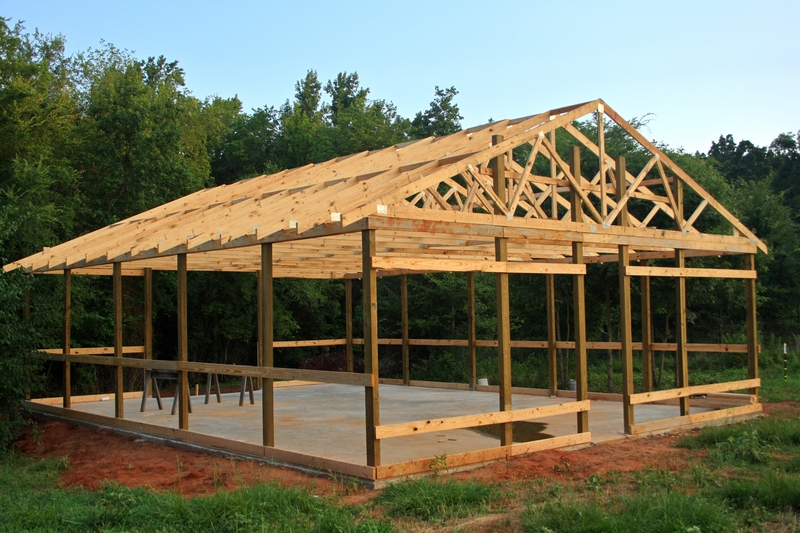
A pole barn, also known as a post-frame building, offers a versatile and cost-effective solution for a wide range of applications, from agricultural storage to workshops and garages. Their simplicity of construction and durability make them a popular choice for homeowners and businesses alike. However, building a custom pole barn requires careful planning and consideration of various factors to ensure a successful outcome. This comprehensive guide [...]
Sunday, November 10, 2024
Diy plans for a quality 12x16 shed
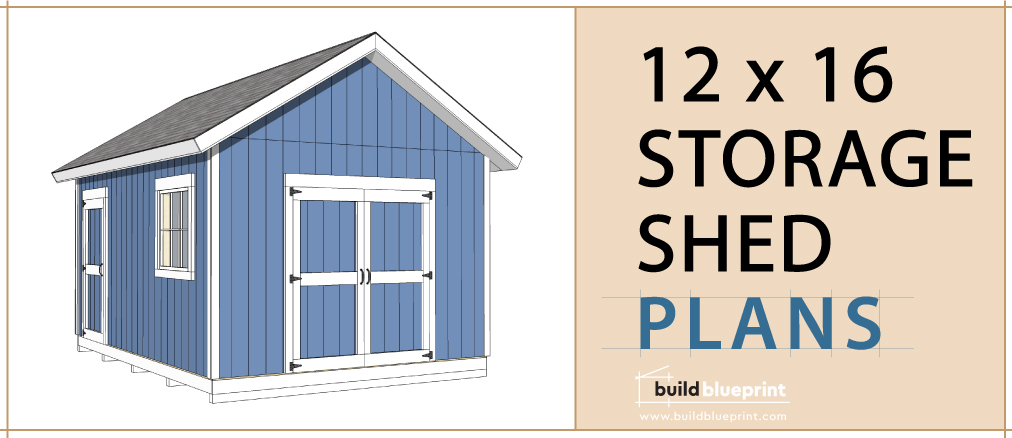
Okay, you've finally decided to take the plunge! A shed. Your very own, personal space. You can use it for anything you want: a workshop, a mini-greenhouse, an art studio, or maybe even a cozy reading nook. But before you start dreaming about all the amazing things you'll do in your new shed, let's talk about building it! Building a 12x16 shed yourself isn't rocket science, but it's definitely a project that requires some planning and elbow [...]
Selecting the right materials with storage shed plans

Alright, you've finally decided to take the plunge and build a shed. The plans are in hand, maybe you even have the location all picked out. Now comes the fun part â€" picking the materials! Don't get overwhelmed by the choices, though. We're here to help you navigate the world of plywood, siding, and shingles, and find the perfect fit for your shed project. Foundation First: Your Shed's Base Think of your shed's foundation as its [...]
How to build a 12x16 shed with minimal experience

Hey there, fellow DIYer! So, you're thinking about building a shed, huh? Maybe you're looking for extra storage, a workspace for your hobbies, or even a tiny oasis to escape the daily grind. A 12x16 shed is a great size â€" spacious enough to be useful, but still manageable for a first-time builder. Don't worry if you're feeling intimidated. I'm here to walk you through every step, from planning to finishing touches, with a beginner-friendly [...]
Budget 8x12 shed designs you can build yourself

Hey there, fellow DIY enthusiasts! Are you yearning for a little extra space, but the thought of those sky-high shed prices makes your wallet cringe? Don't worry, you're not alone! Building your own 8x12 shed can be a fantastic way to get that extra storage you need without breaking the bank. Now, before we dive into the exciting world of shed building, let's be clear: this is a project that requires some elbow grease and a bit of know-how. [...]
Subscribe to:
Posts (Atom)